What is lead time? Definition and strategies to optimize
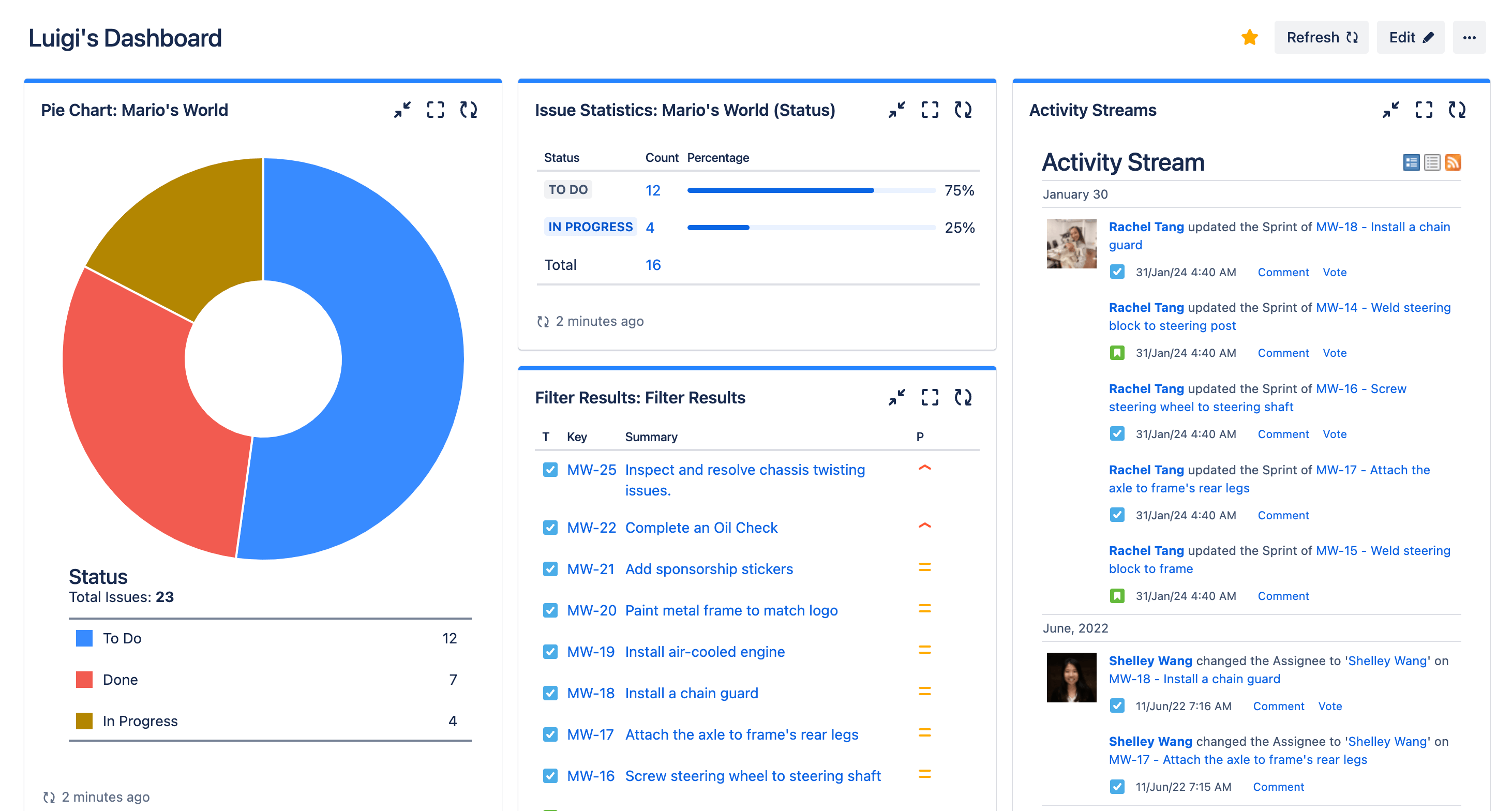
Today’s customers don’t want to wait. When delivering products, long lead times can negatively impact customer satisfaction, regardless of product quality. When faced with the option of waiting months for their preferred product or receiving a comparable alternative immediately, most customers will choose the readily available option.
Optimizing the supply chain can lead to greater resilience, fewer disruptions, defined mitigation plans, and rapid recovery, all of which contribute to shorter lead times. These strategies can help improve overall competitiveness, increase orders, and reduce costs.
This guide defines lead time, discusses the different types of lead times and the formulas for calculating them, and offers tips on reducing lead times in your business.
Definition of lead time
Lead time is the elapsed time from the start of a process to its completion. It can be applied to any process in which a set of actions takes place. For example, a highly customized product, such as a work of art, may have a long lead time due to its unique, customer-centric requirements. Standardized products, such as vacuum cleaners, may have a short lead time due to established production processes and inventory management.
Lead-time metrics are crucial for understanding and optimizing various business processes. They’re an essential part of strategic planning and decision-making, leading to improved customer satisfaction and continuous improvement.
Types of lead time
There are three types of lead time:
- Customer lead time is the time between when a customer places an order and when they receive the product. It often begins with the order confirmation but can include the time to place the order. It encompasses preparing the product, packing, and shipping and ends with the final delivery.
- Material lead time is common in product manufacturing. It measures the time between identifying the need for materials and receiving them. For example, if a manufacturer uses raw steel, the material lead time includes defining the quantity and grade needed, placing the order with the supplier, knowing the supplier’s lead time to make the materials to specifications, packing, and shipping.
- Production lead time is the time it takes to create a product once all raw materials are available. This internal lead-time metric doesn’t include shipping to customers but ends with a product-ready status. For example, production lead time in software development encompasses gathering requirements, crafting design and development specifications, developing software, testing, and releasing.
Though measured separately, you can include these in a cumulative lead time that measures the end-to-end cycle, such as from raw material to the customer’s hands.
Components of lead time
Lead time breaks down into specific elements to help measure, track, and optimize processes. These components include the following:
- Pre-processing encompasses the activities before purchasing materials or products, such as identifying requirements, creating the job or statement of work, and purchasing. These activities precede placing the actual order and can vary by industry.
- Processing includes the time from receiving the order to producing the product. In software development, this is the time to create a new feature. In manufacturing, it’s the time to build the physical product.
- Wait time is the time between pre-processing and processing. For example, if the product is on a strategic roadmap but has projects ahead of it, the wait time indicates the elapsed time between placing the order and when processing begins.
- Storage refers to the amount of time a product is stored in a facility, such as a warehouse, before shipping.
- Transportation is the amount of time a product is in transit, from leaving the warehouse to reaching the customer.
- Inspection is when the customer must verify that the product meets their approval. For manufactured items, this may be testing that the product functions as expected. In software development, this is commonly the user acceptance testing period. In all examples, the inspection time may include making product corrections.
Factors affecting lead time
Many factors can influence lead time, including:
- Supplier availability: Your lead time predictions are only as good as your supplier’s. If the supplier is unable to secure materials, their lead times lengthen.
- Supplier reliability: The quality of the materials your supplier receives can impact your lead time, especially if products need repairs or replacement.
- Production processes: Each step in the production process has the potential to lengthen or shorten lead times. Efficient processes improve lead times, while opaque or complex processes can create longer lead times.
- Inventory levels: Low inventory levels during high demand can lengthen lead times. However, too much inventory that requires storage can also lead to inefficiencies in order processing.
- Transportation: The distance products must travel between your warehouse and your customer, or whether they must clear customs or undergo regulatory inspection, can affect lead times.
- Quality: The reliability of your products and whether they meet customer expectations can result in shipping replacement products. When this happens, the lead time from order to customer roughly doubles.
- Demand: Product demand can be seasonal. For example, if you manufacture patio furniture, demand increases during warm months. If demand outpaces the production process, this can result in backlogged orders. Every moment an order is in backlog, the average lead time increases.
- Communication: Poor communication across teams or with suppliers and shippers can create inefficiencies. This can include orders not shipping when the product is available or a delay in ordering raw materials.
- External events: The Covid pandemic disrupted the supply chain, resulting in long lead times. Other events, such as natural disasters, power outages, road construction, and political events, can also impact lead times.
How to measure lead time
A generic formula for calculating lead time is the process complete date minus the process start date.
For specific lead time types, the formulas are as follows:
- Production lead time is the sum of production time, procurement time, and shipping time.
- Inventory lead time is the sum of supply delay and reordering delay time.
- Order fulfillment lead time is the order delivery date minus the order received date.
Strategies to reduce lead time
You can do many things to reduce lead times, all leading to developing a strategy that measures, tracks, and optimizes each step in your processes. This iterative process is integral to your overall product strategy. Here are some ways to improve your lead times:
Process optimization
Review the processes that contribute to lead time. If there are unnecessary steps or waste, eliminate these. Remember that process optimization may require adding new steps to reduce lead time.
For example, if regulatory reviews affect your lead times, determine the rate of rework your finished products undergo. Assign an individual or team to understand compliance and validate that the specifications meet those requirements. Additional steps like compliance testing for finished products may also help. While these steps may increase production lead time at first, they can decrease the cumulative lead time for your products.
If you’re purchasing raw materials, review the rate of reorder and rejection due to quality issues. Look for opportunities to improve the quality. These can include defining clearer requirements for the materials you need, auditing the quality of various suppliers, and reviewing how you store and use materials.
Automation
Automated reports during project planning and each project management phase can alert you to low inventory, longer-than-usual lead times, fluctuating customer demand, and compliance errors. With tools such as Jira reports, you can track your cycle times and the issues impacting them. For example, a cumulative flow diagram can help you spot blockages in real-time, and a control chart can provide insights into cycle and lead times.
Additional automation steps may include alerts when inventory reaches a certain level, critical errors during product testing, or customer feedback triggers. For smoother delivery, incorporate lead time impact automation as a standard project management function.
Supplier relationship management
Get to know your suppliers, and do your homework. The cheapest products can become the most expensive if they impact your lead times through rework, unreliability, or inconsistent availability. Managing the supplier relationship is critical to procuring quality materials, negotiating prices, and handling rejected or reworked materials.
When selecting suppliers, review their lead times, locations, and reliability. Local suppliers can often deliver more quickly, and proximity allows you to develop better relationships. When a problem occurs, having a strong relationship with your supplier can help you overcome challenges rapidly.
Lean manufacturing techniques
Lean manufacturing is a philosophy and practice developed by Toyota that many businesses have adopted to eliminate waste in their processes. It intends to create the most value for customers using the fewest resources. Lean principles include the following:
- Identify value through value stream mapping. This is an analysis of the value provided to the customer at each step of the process. It allows businesses to see where they’re spending time and resources on activities that offer little or no value and eliminate those activities.
- Create flow by removing bottlenecks and sequencing process steps efficiently from beginning to end.
- Establish pull by producing products based on actual demand. This helps reduce excess inventory by producing only what is necessary and when needed.
Lean principles strive for product and process excellence by building continuous improvement activities in the product development life cycle.
Optimize lead time with Jira
Jira provides real-time insights that can help improve your lead times and overall work management. From forecast management to resolution time tracking, Jira helps teams identify and resolve issues early.
Jira’s agile reporting helps teams identify overcommitment and scope creep in sprints, track progress on burndown charts, and improve work estimates with velocity charts.
Lean and agile environments use Jira to optimize their workflows for continuous delivery and improvement.
Lead time: Frequently asked questions
What is an example of lead time?
Lead time can apply to any product or service. For example, if you’re a real estate broker helping a family purchase a home, you may have the following lead times:
- Researching available properties requires four hours.
- Showing potential homes spans two days.
- Securing an accepted offer can happen in two days.
- Inspection takes 10 days.
- Escrow requires five days.
There may be additional steps with lead times, such as securing financing, negotiating repairs, etc. With an optimized process, the lead time from when the family initiates the buying process to moving into a new home can be as short as 31 days.
What is the difference between lead time and turnaround time?
Lead time and turnaround time measure different activities. Lead time is the elapsed time from start to finish, such as fulfilling a customer order or manufacturing a component part.
Turnaround time measures procedural duration, such as ordering a meal in a restaurant or being seen at a health clinic. In a clinic, the turnaround time is the length of time the patient is at the clinic: checking in, waiting to see the provider, meeting with a physician, and checking out. Lead time is typically shorter and includes more variables; for example, a patient might experience a longer wait if another patient with a more urgent issue is prioritized.
Is lead time the same as delivery time?
Although people use them interchangeably, lead time and delivery time aren’t the same. Lead time is the elapsed time in a defined business process, which can include delivery but doesn’t have to. Delivery time is a more specific term that measures the elapsed time between when a customer places an order and when that order arrives.