Total quality management (TQM): what it is and how it works
Quality is the difference between a business thriving and barely surviving. While most businesses understand its importance, many struggle to deliver the excellence their customers demand. Teams work in silos, processes break down, and quality issues snowball into bigger problems.
These challenges aren't unique to any single industry. Luckily, a proven approach can help companies tackle them systematically: total quality management (TQM). TQM transforms how companies think about and manage quality, turning it from a constant headache into a genuine competitive advantage.
In this guide, we’ll discuss the definition of total quality management and how to implement it in your company. We'll provide practical strategies for improving quality across every department, engaging your entire team in the quality mission, and creating lasting positive change.
Ready to solve your quality challenges once and for all? Use free project timeline template to map out your TQM journey.
What is total quality management?
Total quality management is a company-wide approach to improving and maintaining quality in all aspects of business operations. Unlike traditional quality control, which checks final products, TQM makes everyone responsible for quality — from the CEO to front-line workers.
The roots of TQM stretch back almost 100 years when researchers at Western Electric's Hawthorne plants discovered that involving workers in decision-making dramatically improved productivity. The movement gained momentum in the 1950s when quality experts Edwards Deming and Joseph Juran brought statistical control methods and quality management techniques to Japan.
What started as a manufacturing-focused methodology has since evolved into a comprehensive management approach that spans all industries. From healthcare to software development, businesses worldwide use TQM principles to enhance quality, reduce waste, and boost efficiency.
Principles of TQM
Understanding total quality management principles can help improve your business across all departments, creating a culture of continuous quality improvement. These foundational elements work together to create a comprehensive quality management system. Let's explore each one:
Customer focus
Everything starts and ends with the customer. TQM pushes businesses to understand what their customers actually want and need, not just what they think they want. Understanding customer needs means looking at customer feedback, behavior partners, and evolving expectations.
Companies that excel at total quality management consistently monitor customer satisfaction, anticipate future needs, and adapt their processes to deliver superior value. This focused attention on the customer naturally leads to increased loyalty and long-term business success.
Leadership commitment
Quality initiatives live or die by leadership support. Leaders must set the tone for quality improvement by actively championing TQM principles throughout the business.
This means more than just talking about quality; it requires visible commitment through resource allocation, direct participation in quality initiatives, and consistent reinforcement of quality standards. When leaders demonstrate their dedication to quality through words and actions, it creates a ripple effect throughout the company.
Employee involvement
Quality isn't just management's job — it's everyone's responsibility. TQM thrives when employees at all levels feel empowered to take ownership of quality in their daily work. Businesses should create clear channels for employees to contribute ideas, participate in improvement initiatives, and make decisions about quality in their areas of expertise.
This collaborative approach improves quality outcomes and increases employee engagement and job satisfaction.
Process-oriented approach
Quality outcomes come from quality processes. A process-oriented approach means looking beyond individual tasks to understand how work flows through the company. TQM focuses on optimizing these processes to enhance both quality and efficiency.
By recognizing how different processes interconnect and influence each other, businesses can identify improvement opportunities that might be missed when looking at tasks in isolation.
Continuous improvement
The pursuit of quality never ends. TQM creates a culture where improvement is an ongoing journey rather than a destination. This means constantly seeking feedback, experimenting with innovative approaches, and refining processes based on results. Companies should encourage new ideas, learn from successes and failures, and continuously raise the bar for quality standards.
Data-driven decision-making
Effective quality management requires moving beyond gut feelings to embrace data-driven decision-making. TQM relies heavily on statistical process control, root cause analysis, and other analytical tools to understand performance and guide improvements.
By collecting and analyzing quality metrics, businesses can identify trends, predict potential issues, and decide where to focus improvement efforts.
Integrated system
Quality can't exist in silos. TQM requires a unified approach where all organizational functions and processes align with quality principles. This means creating shared quality standards, coordinating improvement efforts across departments, and ensuring clear communication channels throughout the company. When everyone works together toward common quality goals, the impact is far greater than isolated improvement efforts.
Mutual supplier relationships
Strong, collaborative partnerships with suppliers are essential for maintaining consistent quality throughout the supply chain. Organizations should work closely with suppliers to set clear quality expectations, share feedback, and jointly solve quality challenges. These partnerships help ensure that quality standards are maintained from raw materials through to final products or services.
Benefits of implementing TQM
When done right, TQM delivers significant advantages:
- Higher customer satisfaction and loyalty
- Reduced waste and operational costs
- Better project management efficiency
- Improved project collaboration across teams
- Enhanced project scope definition and control
- Increased employee engagement and satisfaction
- Stronger competitive position
- Better project planning and execution
- Higher product/service quality
Together, these improvements create a powerful competitive advantage. Organizations that successfully implement TQM often pull ahead of competitors still struggling with quality inconsistencies and inefficient processes. The combination of lower costs, higher quality, and greater customer satisfaction enables companies to capture larger market share while maintaining stronger profit margins than their competitors.
How to implement TQM
Breaking TQM into manageable steps can make the process easier, and project management tools like Jira can take the headache out of implementation. Here's what you need to know to implement TQM in your organization:
Assess current quality practices

Thoroughly review your existing quality standards and processes. Document your current workflows and identify where quality issues typically arise. Look for gaps between your current practices and total quality management principles.
Use a Jira kanban board to visualize and track your assessment findings.
Establish goals and create a roadmap
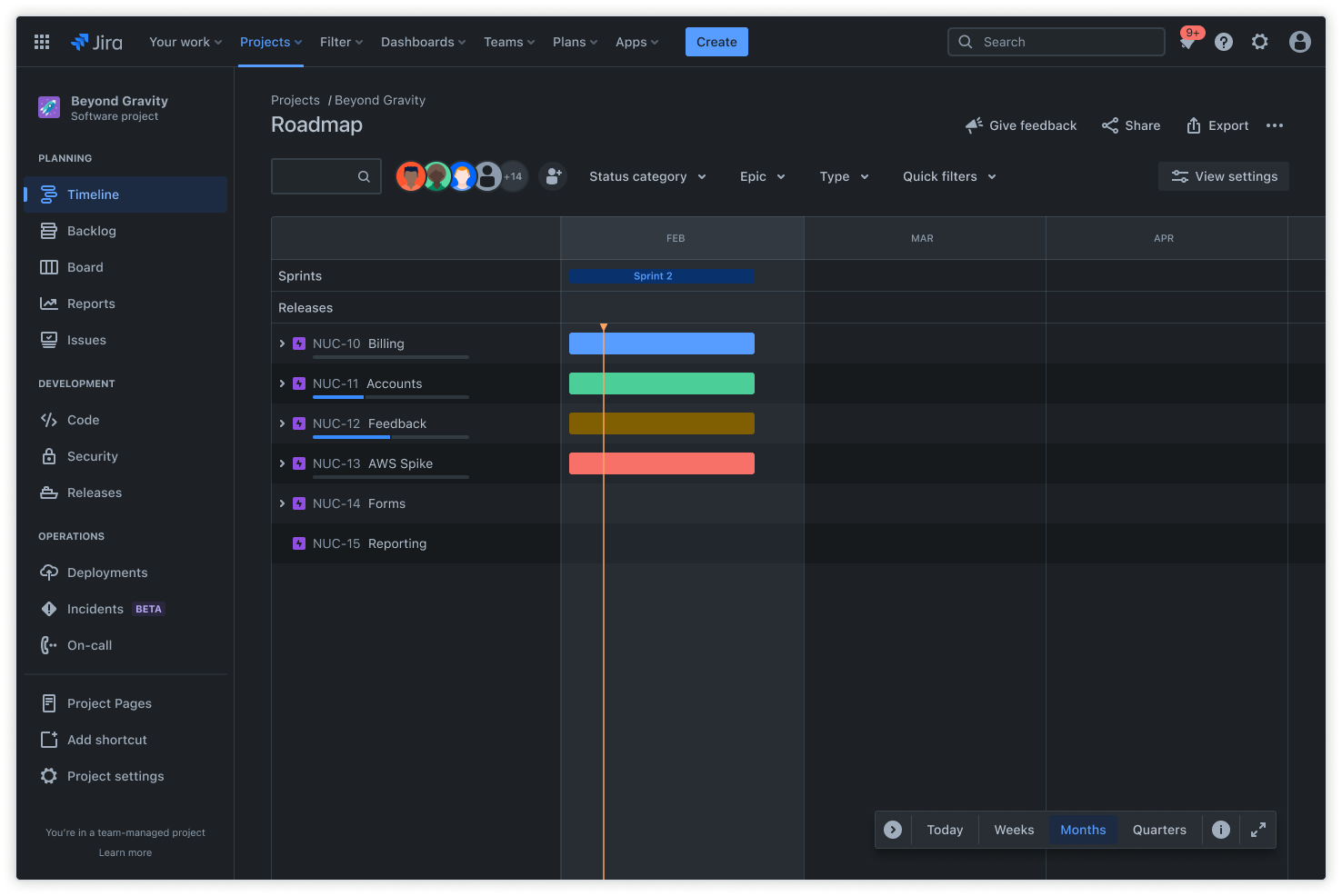
Set specific, measurable quality objectives that align with your organization's project goals. Create a detailed implementation timeline with clear milestones and responsibilities.
Use free project timeline template to map out your quality journey.
Train employees
Develop a comprehensive training program covering total quality management principles and techniques. Focus on building practical skills that employees can apply in their daily work. Create opportunities for hands-on learning and collaborative problem-solving.
Monitor progress and refine strategies
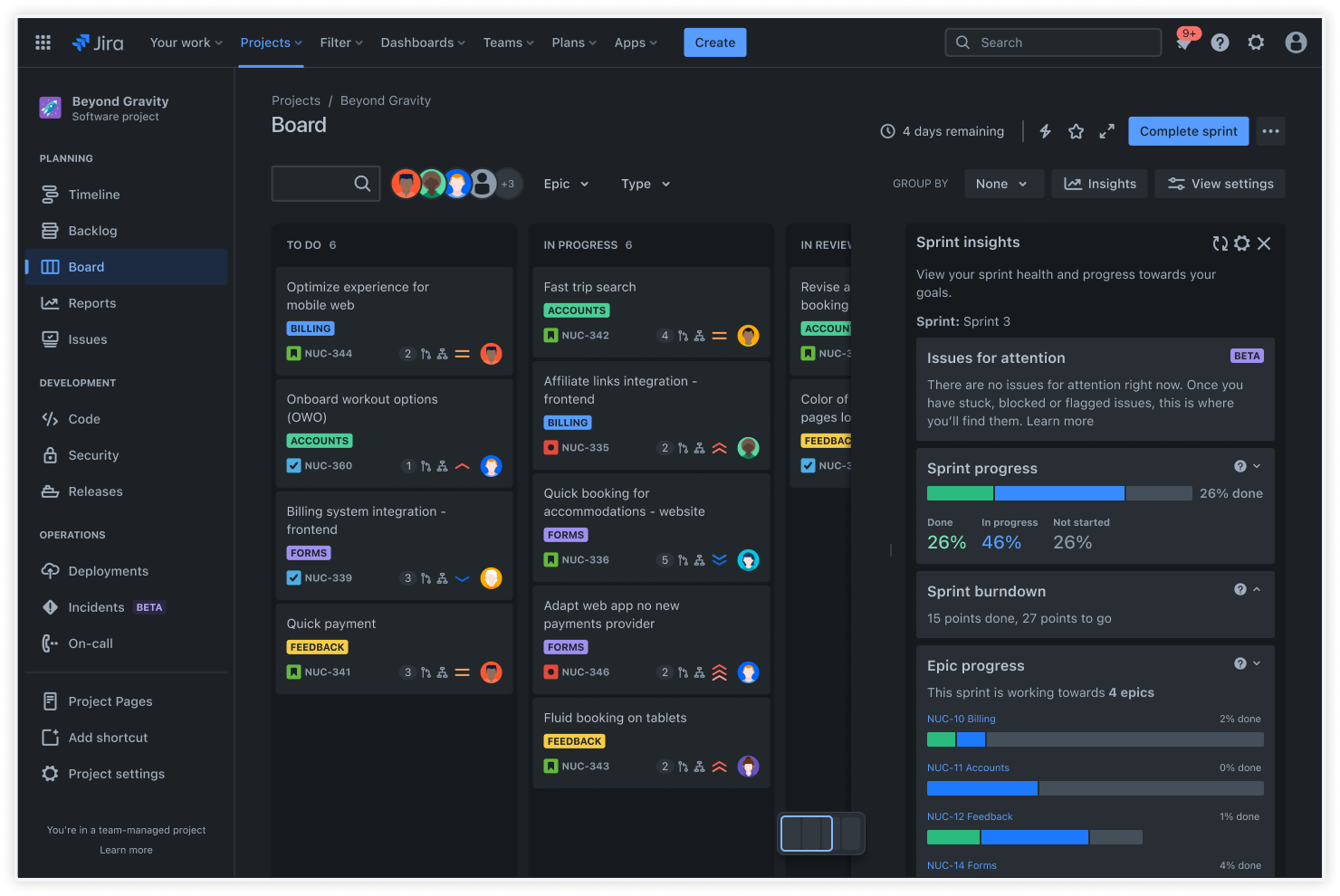
Track your progress using data-driven tools like Jira insights. Review performance metrics regularly and gather feedback from all stakeholders. Adjust your TQM strategy based on what's working and needs improvement.
Need a structured way to document and manage your TQM implementation?
Pros and cons of TQM
Before implementing TQM practices, you should understand its benefits and potential drawbacks. While the advantages often outweigh the challenges for most organizations, being aware of both sides helps you prepare for a simple implementation.
Benefits of TQM are:
- Improved product and service quality: Organizations see fewer output defects and errors. Quality becomes consistent and predictable rather than hit-or-miss.
- Greater customer satisfaction: When quality improves, customers notice. They experience fewer issues with products and services, leading to increased loyalty and repeat business.
- Reduced costs through efficiency: Fewer mistakes mean less rework and waste. Organizations typically see significant savings in time and materials once TQM takes hold.
- Better employee engagement: Staff involved in the quality process feel more empowered and invested in their work.
- Enhanced market reputation: Word spreads when you consistently deliver quality. Organizations often find themselves becoming the go-to choice in their market.
While the benefits are compelling, you should recognize that implementing TQM isn't always smooth sailing. Organizations often face several hurdles along the way, such as:
- Significant time and resource investment: TQM requires substantial upfront investment in training, tools, and processes. Organizations must be prepared for the financial and time commitments involved.
- Cultural change difficulties: Shifting from traditional quality control to TQM requires a fundamental change in how people think and work. Some employees may resist these changes, making the transition challenging.
- Delayed results: TQM is a long-term strategy, not a quick fix. Organizations typically don't see significant improvements for six months to a year after implementation begins.
- Need for consistent commitment: Success requires unwavering support from leadership and steady effort from everyone involved. Many organizations struggle when enthusiasm wanes after the initial push.
Example of TQM
To help you understand what total quality management looks like in practice, let's take a look at how a software development company might use it:
Before implementing TQM, the company struggled with standard software development challenges: delayed releases, inconsistent code quality, and growing customer complaints about bugs. Therefore, they decided to implement TQM throughout the entire development process, from initial design to customer support.
Here's how they might put TQM principles into action:
- Create cross-functional quality circles: The company might form teams that include developers, testers, customer support reps, and product managers. These teams would meet weekly to identify quality issues and propose solutions.
- Implement regular code reviews: They might establish a peer review system where at least two other developers review all code changes before deployment. This can catch potential issues early and help spread best practices throughout the team.
- Use tools to manage project deadlines: They could use time management tools and project tracking software to monitor deadlines and resources, helping teams deliver quality work on schedule.
- Track customer feedback: The development company might implement a comprehensive feedback system to collect and categorize all customer reports, feature requests, and complaints. This data directly informs development priorities and quality improvements.
- Use data analytics to identify bug patterns: They can develop a system to analyze bug reports and identify common patterns, allowing them to address root causes rather than just symptoms. This approach can prevent similar issues from recurring.
After implementing these TQM practices, the software development company might measure the results and find a reduction in customer-reported bugs, faster development cycles, improved customer satisfaction scores, and reduced development costs.
The best part is that these improvements aren't just temporary wins. The company can maintain and build upon these gains by refining its total quality management practices.
Use Jira to streamline total quality management
Getting started with TQM doesn't have to be complicated. Jira provides all the necessary tools in one place, making it simple to track quality projects and keep your team on the same page. You can set up workflows that match your team's work, and everyone can easily see what needs to be done next.
The best part? Jira's features fit naturally with quality management. You can use kanban boards to spot workflow problems before they slow you down, check your progress with Jira insights, and plan your work on a Jira timeline.